Do the complexities of construction material logistics leave you scratching your head? Have you faced the frustration of delayed lumber delivery, causing your project timelines to stretch on indefinitely? You’re not alone.
For contractors, managing the timing and delivery of lumber materials is a critical piece of the construction puzzle. This is ultimately because time is money in the construction industry, and material management inefficiencies can lead to extended timelines and an uptick in cost. Coming full circle, this leg of the industry can feel like a high-wire act. But the good news is that’s where strategic material management comes into play. After all, it’s not just about having the right materials; it’s about managing them effectively.
Why is Materials Management Crucial?
Proper lumber delivery and materials management go beyond mere logistics; they underpin the success or failure of a construction project. They affect everything, from budget to build quality to timelines and team morale. It’s an umbrella aspect of business designed to ensure resources and labor flow seamlessly in sync.
In short, without an overarching strategy for material management, contractors can face over-ordering, excessive waste, theft, damage, and the spiraling operational costs that follow. Moreover, these physical resources are tied closely to the financial foundation on which construction businesses build their futures.
How can you improve and ensure your project remains structured, efficient, and cost-effective?
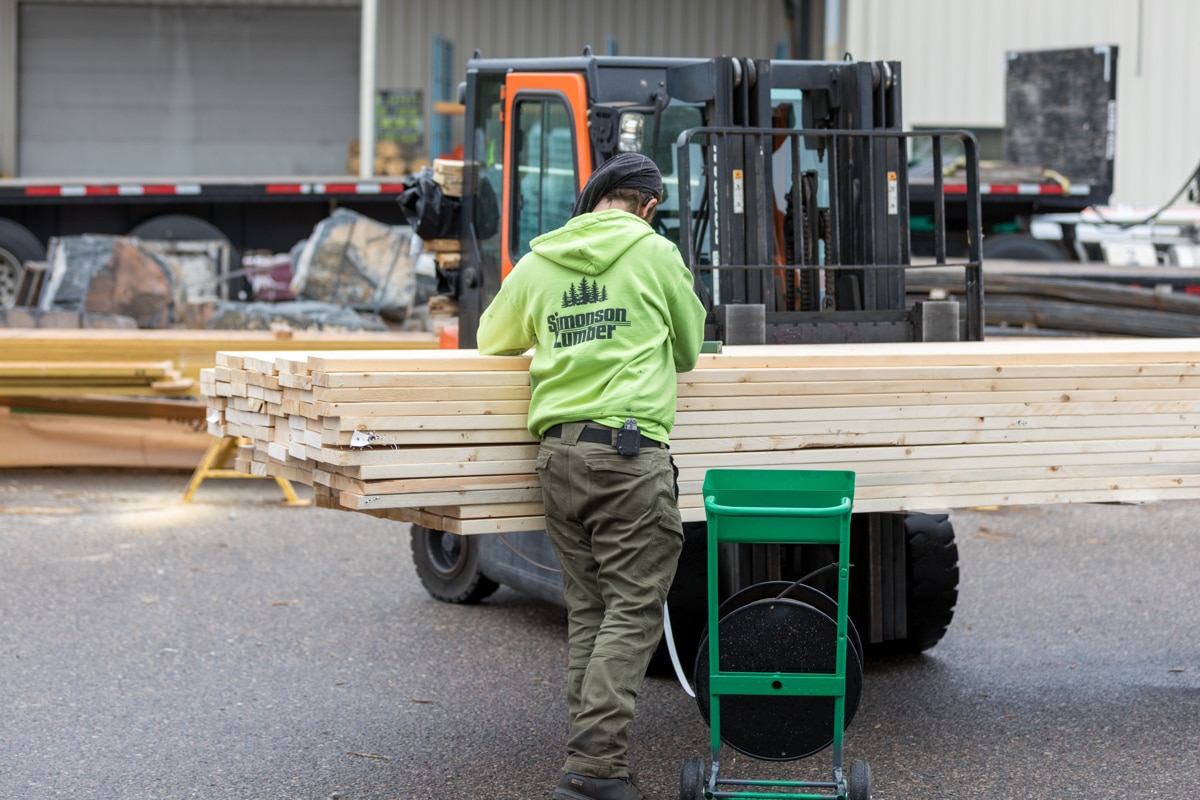
5 Tips for Lumber Delivery and Construction Material Management
Tip 1: Plan Your Space and Storage
Before the first piece of lumber is delivered, have a detailed plan for where materials will be stored. Assess the space you have available on your job site and designate specific areas for different types of materials. Weather-protective measures may also be necessary, especially for sensitive materials. By organizing your space efficiently, you can eliminate job delays caused by inaccessible or damaged materials.
Remember, storage isn’t just about stacking lumber out of the way. Properly sorting and securing the materials to protect them from the elements and job-site accidents is key. Keep in mind that it’s good practice to elevate lumber off the ground to avoid moisture damage, cover it with tarps, or store it in temporary sheds if prolonged exposure to weather is anticipated.
Tip 2: Coordinate Deliveries with Your Schedule
Timing is everything in construction, and lumber delivery should be carefully coordinated with your project’s timeline. Communicate clearly with the delivery company about not just the dates but specific times when materials should arrive. This minimizes periods where materials lay unused and reduces the risk of theft or damage.
Work closely with your sales manager to optimize this and consider implementing Just-In-Time delivery methods for greater efficiency. Just-In-Time delivery is a process that reduces the need for storage space and limits potential material degradation. However, this requires accurate project forecasting and solid communication with your supplier to ensure precision.
Tip 3: Inspect Materials Upon Arrival
Conducting a thorough inspection of materials upon arrival is a step that should never be skipped. Ensure all items received match what was ordered in type, quality, and quantity. Discrepancies can lead to significant setbacks. If there are any issues, it’s crucial to address them immediately with the supplier to rectify potential problems quickly.
Designate a trusted team member to handle material inspections and maintain a consistent method for checking and recording the inventory. This process helps with future ordering, project management accuracy, and maintaining a working relationship with suppliers through accountability.
Tip 4: Utilize Efficient Handling Equipment
The right tools make any job easier and safer. The same applies to material handling on a construction site. Investing in or renting the appropriate equipment for moving heavy loads reduces the physical strain on workers and increases productivity. Forklifts, pallet jacks, and even conveyors can be invaluable, depending on the project’s size and the material volume.
Proper training for handling equipment is just as essential as the equipment itself. Ensure that personnel operating such machinery are certified and understand how to use it safely within the job site environment.
Tip 5: Find a Full-Service Lumber Yard Partner
It goes without saying, but the ultimate experience and capstone for successful material management is connecting with a dependable partner. A reliable partner like Simonson Lumber understands the importance of schedules, provides high-quality materials, and offers exceptional customer service to make every aspect of lumber delivery and material management seamless.
The success and effectiveness of every tip above and then some all boil down to choosing the right partner who is invested in your project’s success. This partnership means you spend less time worrying about managing materials, build confidence in your processes, and gain more time focusing on the aspects of construction that demand your attention the most.
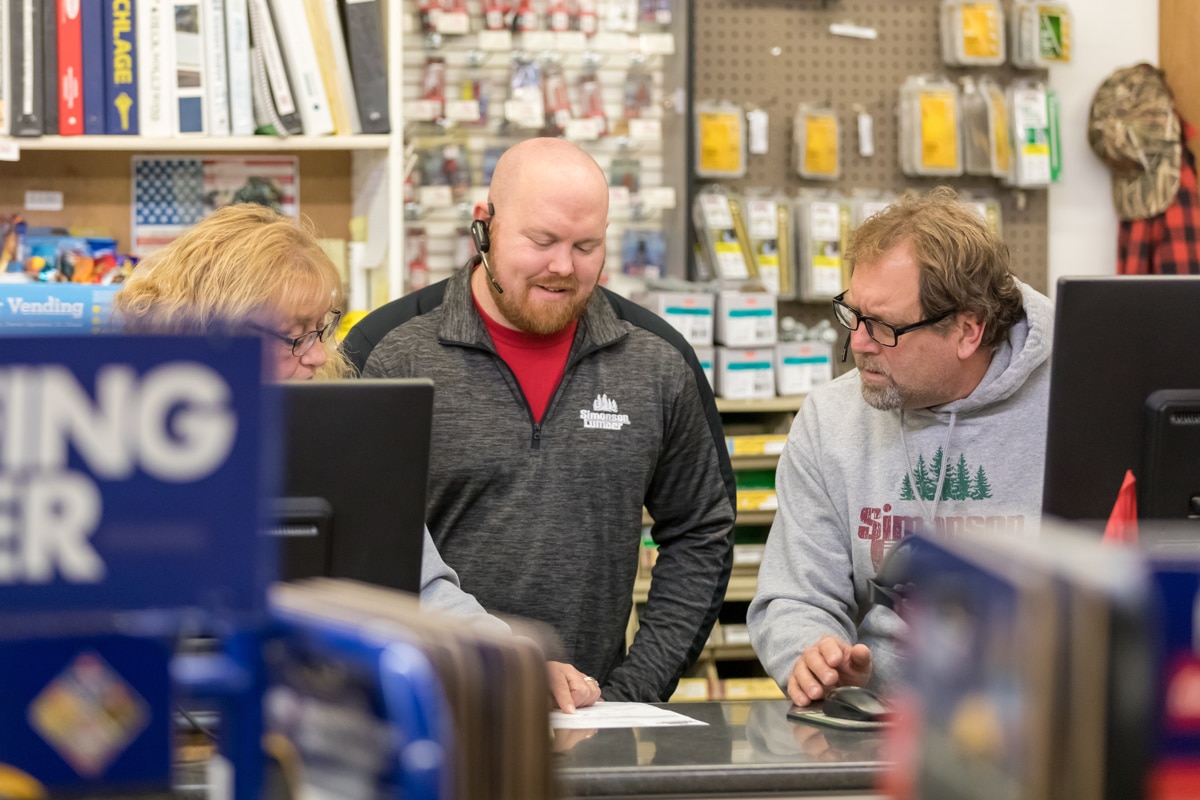
Manage Smarter, Build Better with Simonson Lumber
Every construction project has its hurdles, but with these strategies for robust lumber delivery and material management, you’re setting up for success. From accurate scheduling and job site organization to the quality of lumber and the importance of a trusted partnership, managing your construction materials effectively sets the foundation for a successful build.
Where you need it, when you need it. Ready to take your project to the next level? Contact Simonson Lumber today and experience the advantage of a lumber delivery service that values quality, efficiency, and reliability just as much as you do.